Breathing new life to Ellenex's positive pressure monitoring in data centers, PDT2
- Andrae Navaratne
- Oct 27, 2023
- 4 min read
In today's fast-paced industrial landscape, efficiency and reliability are paramount. Ensuring the continuous and optimal performance of their pneumatic systems, was a critical challenge.

Client: Global Data Center
Technology: LoRaWAN
In this success story, we will delve into the remarkable journey of how Ellenex transformed our client's operations by implementing cutting-edge positive pressure monitoring technology for cabinet monitoring of their server racks.
Our client operates a high-capacity data center that heavily demands an accurate monitoring system, to monitor the pressure and temperature of the cabinet server racks. The challenge they faced was the lack of near real-time insights into the data center's health and efficiency. Frequent downtime, unexpected breakdowns, and soaring maintenance costs were crippling their operations. The client needed a solution that could offer predictive maintenance capabilities and optimize performance.
According to a report from the U.S. Department of Energy, data centers can consume 100 to 200 times more electricity than standard office spaces. Efficient cooling, which includes maintaining positive pressure, is a critical factor in reducing this energy consumption.
Monitoring positive pressure inside data center racks is essential for several reasons, including increasing the life and fan performance of the equipment. Positive pressure refers to maintaining a higher air pressure inside the data center racks than in the surrounding environment. Here are some key points to understand the importance of monitoring positive pressure:
Efficient Cooling: Data center equipment, such as servers, switches, and storage devices, generates a significant amount of heat during operation. Maintaining positive pressure ensures that cool air is forced into the racks, allowing for efficient cooling of the equipment. This helps prevent overheating, which can lead to equipment failures and downtime.
Preventing Contaminants: Positive pressure helps keep contaminants, such as dust and particulate matter, from entering the racks. Dust and debris can clog fans and heat sinks, reducing their efficiency and lifespan. By maintaining positive pressure, you can create a barrier that prevents outside air and contaminants from infiltrating the equipment.
Optimizing Fan Performance: Fans play a crucial role in cooling data center equipment. When positive pressure is maintained, fans can work more efficiently because they have a consistent and well-directed airflow. This improves the overall performance of fans and extends their lifespan, reducing the need for frequent replacements.
Energy Efficiency: Monitoring positive pressure and ensuring proper airflow management can lead to significant energy savings. When cooling systems are more efficient due to positive pressure, less energy is required to maintain the desired temperature within the data center. This can result in lower energy costs and a reduced carbon footprint.
Equipment Reliability: Maintaining a controlled environment with positive pressure helps enhance the reliability and longevity of data center equipment. Lower temperatures and reduced exposure to contaminants contribute to the overall health of the hardware, reducing the risk of unexpected failures.
Compliance and Safety: Many industry standards and regulations require data centers to maintain specific environmental conditions, including temperature and air quality. Monitoring positive pressure helps ensure compliance with these standards, which can be crucial for businesses in regulated industries.
Ellenex stepped in with a comprehensive solution powered by its state-of-the-art performance monitoring platform. The two unique features that stood out were:
Near Real-time Data: Near real-time monitoring and visualization, allow the client to track the performance of each server rack unit continuously.
Sensor Technology: Ellenex PDT2-L: Differential Pressure Sensor - With built-in Temperature Sensor allowed the client to gather both pressure and temperature data, for predictive maintenance purposes to avoid costly unplanned downtime.
Implementing the solution was not without its hurdles. Ellenex faced challenges such as integrating with the client's existing infrastructure and educating the workforce on the new system. However, Ellenex's differentiator became apparent here—its robust, end-to-end remote monitoring adaptability and scalability seamlessly integrated with the client's setup. This amalgamation allowed our client to gain actionable insights from the vast amount of data collected in near real-time. The added value of this technology was profound: reduced maintenance costs, increased server lifespan, and improved overall operational efficiency. Ellenex collaborated closely with the client to ensure a smooth transition. The results were nothing short of remarkable:
Reduction in Maintenance Costs: Predictive maintenance reduced unplanned downtime and maintenance expenses significantly.
Increase in Server Lifespan: By identifying and rectifying issues in near real-time, the servers lasted longer, saving on replacements.
Enhanced Productivity: With reliable monitoring, our client's data centers ran smoothly, leading to increased output and satisfaction.
A study by the Ponemon Institute found that the average cost of data center downtime in 2020 was approximately $740,000 per incident. Proper cooling and environmental control, which positive pressure contributes to, can help reduce the risk of unplanned downtime.
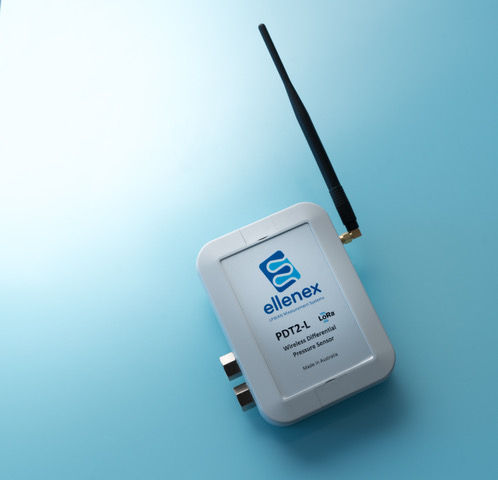
In conclusion, Ellenex's performance monitoring solution revolutionized our client's operations, setting new standards for efficiency and reliability in the industry. This success story underscores the importance of leveraging cutting-edge technology to address near real-world challenges and achieve lasting success in the industrial sector. Ellenex remains committed to driving innovation and enabling industries to thrive in an ever-evolving landscape. The partnership between Ellenex and our client serves as a testament to the transformative power of technology in addressing the unique challenges of the industrial sector.