Ditch the Dust Why Flush-Type Pressure Sensor is a Game-Changer in FMCG
- Mohan Krishna Polavarapu
- Oct 9, 2023
- 3 min read
In the fast-paced world of Fast-Moving Consumer Goods (FMCG) manufacturing in India, efficiency and precision are paramount. Every aspect of the production process must be optimized to meet the demands of a dynamic market. One often overlooked yet crucial aspect is pressure sensing. To maintain production quality and efficiency, measuring pressure accurately and reliably is essential, especially when dealing with live lines. However, many manufacturing plants in India face a common challenge—dust and contaminants that can wreak havoc on equipment and processes.
A report by the Federation of Indian Chambers of Commerce & Industry (FICCI) highlighted that 60% of FMCG manufacturers in India reported equipment downtime as a major concern, affecting both productivity and profitability

Client: One of the largest FMCG manufacturers
Partner: SenRa
Technology used: LoRaWAN
The Challenge of Dust and Contamination
India's industrial landscape, like many other regions, faces environmental challenges. Dust and contaminants are ubiquitous, and in FMCG manufacturing, they pose a significant threat to equipment and processes. Standard pressure sensors, while effective in many applications, have a potential vulnerability—their process ports. These ports can become clogged with dust and debris over time, leading to inaccurate readings and increased maintenance requirements. In a high-speed production environment, downtime is costly, and maintenance interruptions are not an option.
The Solution: Flush-Type Pressure Sensors
Recognizing the need for a more robust solution, the use of flush-type pressure sensors comes into play. These sensors are designed with a flat, flush diaphragm that eliminates the risk of dust and contaminants accumulating in the process port. Here's why they are the ideal choice for FMCG applications in India:
1. Dust-Proof Design
Flush-type sensors are inherently dust-proof due to their design. The absence of a recessed process port ensures that dust and contaminants cannot accumulate, eliminating the risk of measurement inaccuracies.
2. Reduced Maintenance
In an FMCG facility, minimizing downtime is crucial. Flush-type sensors drastically reduce maintenance requirements, as there is no need for regular cleaning or unclogging of process ports. This translates to increased operational uptime and cost savings.
3. Enhanced Accuracy
Accurate pressure measurements are vital for maintaining product quality and consistency. Flush-type sensors provide reliable readings without the interference of dust, ensuring that production processes run smoothly.
4. Longevity
Flush-type sensors are built to last. Their rugged construction and resistance to environmental factors make them a durable choice for demanding industrial environments.
5. Versatility
These sensors can be adapted to various applications within the FMCG industry, from monitoring liquid levels to ensuring precise pressure control in packaging processes.

LPWAN Devices: A Game-Changer
In addition to flush-type pressure sensors, the integration of LPWAN (Low-Power Wide-Area Network) devices can bring transformative benefits, especially in an economy as big as India:
1. Cost-Effective Connectivity
LPWAN technology offers cost-effective, long-range communication. It allows manufacturers to connect sensors, across large industrial facilities without the need for extensive infrastructure investment.
2. Remote Monitoring
LPWAN enables real-time remote monitoring of critical parameters like pressure, temperature, and humidity. This is particularly valuable in developing countries, where skilled personnel may not always be readily available on-site.
3. Predictive Maintenance
By continuously collecting data from sensors, LPWAN devices facilitate predictive maintenance. Manufacturers can proactively address issues, reducing downtime and maintenance costs.
4. Scalability
LPWAN networks can be easily scaled as manufacturing operations grow. This scalability is vital in developing countries where industries are expanding rapidly.
5. Energy Efficiency
LPWAN devices are energy-efficient, with long battery life. This is crucial in regions with unreliable power sources.
The Customer's Journey
In a real-world scenario, a customer in India faced pressure measurement challenges in their FMCG production line. Initially, they considered using a standard pressure sensor, unaware of the unique challenges posed by dust and contaminants in their manufacturing plant. However, after understanding the application's intricacies, they made a wise choice by opting for flush-type pressure sensors and integrating LPWAN devices.
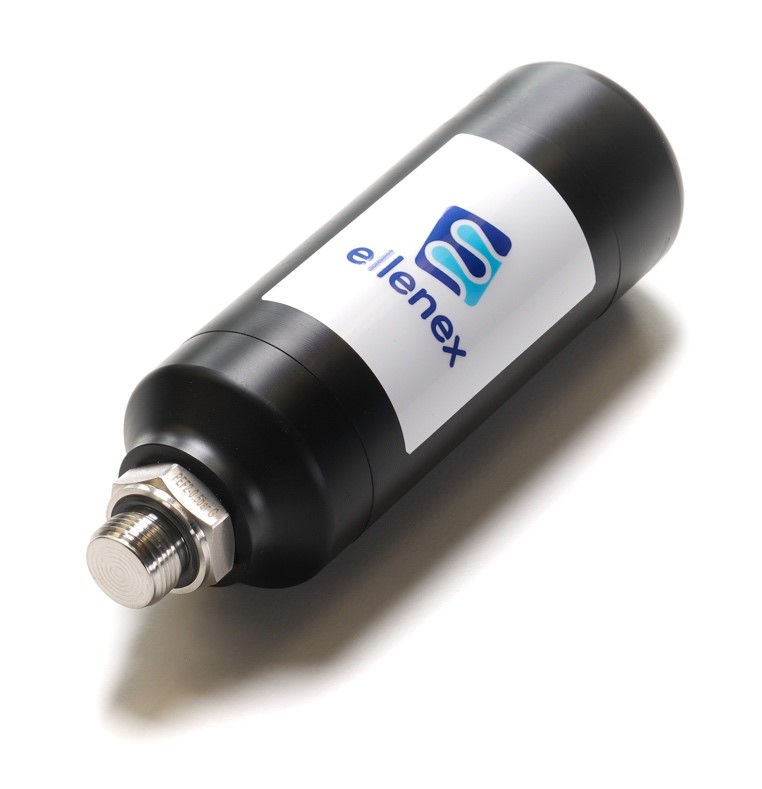
This decision not only addressed the dust-related issues but also allowed them to monitor pressure data remotely and implement predictive maintenance measures. In a fast-paced FMCG environment, where every minute of downtime matters, this change proved to be a game-changer. The customer experienced improved accuracy, reduced operational interruptions, and a more cost-effective solution.
In the competitive world of FMCG manufacturing in India, precision and reliability are paramount. Flush-type pressure sensors offer a solution that ensures accurate pressure measurements, reduces maintenance hassles, and enhances overall production efficiency. By making the switch to these innovative sensors and leveraging LPWAN technology, businesses can stay ahead in the race for efficiency and quality in this dynamic industry.
When it comes to pressure sensing in FMCG applications, remember that not all sensors are created equal. Choosing the right technology, such as flush-type pressure sensors and LPWAN devices, can make all the difference in maintaining a smooth and cost-effective production process in India's fast-moving consumer goods sector. Combatting dust challenges and enhancing connectivity through LPWAN has never been easier, ensuring that your FMCG manufacturing operations stay efficient, reliable, and well-connected.